The importance of choosing a waterproof backpack factory. Choosing a suitable waterproof backpack factory has a profound impact on product quality and business development. From the perspective of product quality, high-quality waterproof backpack factories have advanced production processes and strict quality control systems. In the selection of waterproof materials, they can accurately distinguish and ensure that the fabrics used not only have excellent waterproof performance, but also consider durability and comfort. For example, some high-end waterproof backpack factories use professional PVC/TPU fabrics, which have excellent waterproof and breathable properties and can effectively improve the quality of backpacks. At the same time, exquisite sewing techniques and mature waterproof treatment technology can ensure that the seams of the backpack are tightly waterproof, reducing the risk of water leakage and creating high-quality waterproof backpack products. From the perspective of enterprise development, a suitable waterproof backpack factory is a solid backing for the enterprise. On the one hand, stable and reliable factories can complete order production tasks on time and with quality, ensuring timely supply of products, which helps enterprises maintain good market reputation and customer relationships. For example, before the peak sales season arrives, the efficient production capacity of the factory can ensure that the enterprise has sufficient goods to put into the market and seize business opportunities. On the other hand, excellent factories can leverage their technological advantages and cost control capabilities to provide more competitive product prices for enterprises, helping them stand out in market competition, expand market share, and achieve sustainable development. The purpose of this article is to thoroughly and comprehensively explore the basic elements involved in selecting a waterproof backpack factory. By analyzing multiple dimensions such as factory scale and production capacity, technological strength and process level, quality control system, supply chain management capability, as well as corporate reputation and cooperation attitude, this study provides systematic and professional reference for enterprises or individuals who are interested in seeking waterproof backpack production partners, helping them make scientific and reasonable decisions, find high-quality waterproof backpack factories that meet their own needs, ensure product quality, improve production efficiency, reduce operating costs, and establish long-term stable cooperative relationships to promote the healthy development of the entire waterproof backpack industry. Capacity matching is a crucial factor that cannot be ignored when selecting waterproof backpack factories. It directly affects the smooth execution of orders and the long-term stability of cooperative relationships. For brand owners or distributors, there are significant fluctuations in order volumes across different periods. During peak sales seasons, such as outdoor product exhibitions and tourist seasons, the demand for waterproof backpacks in the market will sharply increase, and the order volume may reach several times or even more than usual; During the off-season of sales, the order volume is relatively low. This requires factories to have the ability to flexibly adjust their production scale to adapt to these dynamic changes. If the factory has insufficient production capacity and cannot deliver sufficient quantities of products on time during peak order periods, it will result in delivery delays. This not only causes companies to miss sales opportunities and damage their market reputation, but may also face risks such as customer claims. On the contrary, if the factory has overcapacity and the enterprise has limited order volume, the factory may increase the unit price of products to share the cost in order to maintain operation, which will undoubtedly increase the procurement cost of the enterprise and weaken the market competitiveness of the products. In addition, capacity matching is not just about matching quantities, but also involves coordinating production cycles. Some complex styles of waterproof backpacks have relatively long production cycles due to their unique design and high craftsmanship requirements. The factory needs to arrange production plans reasonably to ensure the completion of order production within the specified time. Otherwise, even if the factory’s theoretical production capacity can meet the order quantity, it will still be unable to deliver products on time due to the long production cycle. Therefore, when choosing a waterproof backpack factory, enterprises must accurately estimate and analyze their own order demand, including the trend of order volume changes in different seasons and sales channels. At the same time, gaining a deep understanding of the factory’s actual production capacity, maximum capacity, and the range of capacity flexibility ensures a high degree of matching between the two parties in terms of capacity, laying a solid foundation for stable and efficient cooperation. The evaluation of factory scale has a multidimensional impact on production efficiency and quality control, which is an extremely important consideration when selecting a waterproof backpack factory. Large scale factories usually have higher production efficiency. On the one hand, large-scale means the concentration and integration of resources, which can achieve high specialization and standardization of production processes. For example, large waterproof backpack factories often have multiple automated production lines, from cutting and sewing of raw materials to final assembly, each link is handled by professional workers and advanced equipment, with clear division of labor, greatly reducing time waste in the production process and increasing output per unit time. On the other hand, large-scale factories have stronger bargaining power when purchasing raw materials, and can obtain a large amount of high-quality materials at lower prices. This not only reduces production costs, but also ensures stable supply of raw materials, avoiding production stagnation caused by raw material shortages and further improving production efficiency. In terms of quality control, large-scale factories also have certain advantages. They usually have more comprehensive quality monitoring systems and professional quality inspection teams. Large scale production enables factories to invest more resources in purchasing and updating quality inspection equipment, and to strictly control every aspect of the production process, from raw material inspection to finished product sampling, to ensure that products meet high quality requirements. Moreover, large-scale factories often focus on their own brand image and market reputation, and are well aware of the importance of product quality for the long-term development of the enterprise. Therefore, they are more rigorous in quality control. However, small-scale factories are not without advantages. Small scale factories excel in production flexibility and are able to respond more quickly to customers’ personalized needs. For some customized waterproof backpack orders, small-scale factories can adjust production plans and processes more quickly to meet customers’ special design requirements and small batch production needs. In terms of quality control, although small-scale factories have relatively limited resources, due to their small production scale, management can more directly participate in the production process, supervise and control product quality more carefully, and sometimes ensure the stability of product quality to a certain extent. In summary, both large and small factory scales have their own advantages and disadvantages. When evaluating the size of a factory, companies need to consider their own order characteristics and needs comprehensively. If the enterprise has a large order volume and a high degree of product standardization, large-scale factories may be more suitable, which can achieve efficient production and cost control while ensuring quality; If a company has a high demand for customization and small batch orders, the flexibility of small-scale factories may better meet the company’s special requirements. Modern production line configuration is crucial for the manufacturing of waterproof backpacks. Modern production lines are a key indicator for measuring the manufacturing level of waterproof backpack factories, and have a profound impact on product quality, production efficiency, and cost control. In terms of product quality, modern production lines equipped with high-precision production equipment and advanced process control systems can significantly improve the precision and stability of waterproof backpack manufacturing. Taking the cutting process as an example, traditional manual cutting may result in dimensional deviations due to human factors, while modern CNC cutting equipment, with precise program settings, can control cutting errors within a very small range, ensuring the accurate size of each backpack component and providing a good foundation for subsequent sewing and assembly. In the waterproof treatment process, advanced production lines use automated waterproof coating spraying or impregnation equipment to evenly attach waterproof materials to the surface of backpacks, ensuring consistency and reliability of waterproof effects. At the same time, the online detection device in the production line can monitor various parameters in real time during the production process. Once quality problems are found, an alarm will be immediately issued and adjustments will be made, effectively reducing the defect rate and improving the overall quality of the product. Production efficiency is also a major advantage of modern production lines. Automated production equipment has fast operating speed and strong continuous working ability, which can greatly shorten the production time of a single waterproof backpack. For example, automatic sewing robots can quickly and accurately complete backpack sewing work, with much higher work efficiency than manual sewing, and can work continuously for a long time. In addition, modern production lines achieve rapid circulation of raw materials, semi-finished products, and finished products between various production links through intelligent logistics conveying systems, reducing material waiting time and further improving overall production efficiency. This enables the factory to complete a large number of production tasks in a shorter period of time, meeting the market’s demand for waterproof backpacks. Cost control also relies on modern production lines. On the one hand, the introduction of automation equipment reduces reliance on a large amount of manual labor and lowers labor costs. Although the initial investment in purchasing automation equipment is relatively large, in the long run, its operating costs are relatively low, and it can bring greater economic benefits by improving production efficiency and product quality. On the other hand, the precision production and strict quality control of modern production lines reduce material waste and additional costs caused by defective products and rework. At the same time, efficient production processes also reduce indirect costs such as energy consumption, improving the factory’s cost competitiveness. In summary, modern production lines play an irreplaceable role in the manufacturing process of waterproof backpacks. Factories with advanced production lines can achieve efficient production and cost optimization while ensuring product quality, providing enterprises with more competitive products. Therefore, when selecting a waterproof backpack factory, enterprises should focus on examining the production line configuration of the factory to ensure that it has modern production capacity to meet their requirements for product quality and production efficiency. Waterproof technology capability, waterproof material application capability. In terms of waterproof material application, professional waterproof backpack factories need to keep up with the forefront of the industry, be familiar with and able to use various new materials reasonably. There are various types of waterproof materials on the market today, ranging from traditional coating materials to high-performance waterproof films, each with its unique performance characteristics and applicable scenarios. High quality factories should be able to accurately select the most suitable waterproof materials based on the different usage scenarios, positioning, and customer needs of backpacks. For example, for waterproof backpacks commonly used by outdoor sports enthusiasts, factories may choose fabrics with high waterproof levels and good breathability, such as eVent fabric, which not only effectively blocks rainwater infiltration, but also allows the water vapor emitted by the human body to be discharged, keeping the inside of the backpack dry and comfortable. For waterproof backpacks used for daily leisure purposes, while ensuring certain waterproof performance, materials that focus more on lightweight and cost-effectiveness may be chosen. In addition, factories also need to master the processing characteristics of different materials to ensure that the performance advantages of materials are fully utilized in the production process. Some waterproof materials have strict requirements for processing temperature, pressure, and other conditions. Factories must have corresponding process control capabilities to ensure the perfect combination of materials and backpacks and achieve the best waterproof effect. The level of waterproof technology is a key factor in determining the waterproof performance of waterproof backpacks. Advanced waterproof technology can ensure that backpacks maintain good waterproof performance in various harsh environments. Hot press sealing technology is currently a common and effective waterproofing process, which tightly adheres the waterproof tape to the seam of the backpack through high temperature and high pressure, forming a seamless seal and effectively preventing moisture from entering. Professional factories strictly control parameters such as temperature, pressure, and time during hot press sealing to ensure stable and reliable sealing quality. There is also a waterproof coating process, which requires the factory to evenly apply the waterproof coating on the surface of the backpack, with a moderate thickness and no leakage. The quality and uniformity of the coating directly affect the waterproof effect and the service life of the backpack. Some high-end factories use electrostatic spraying technology, which utilizes the principle of electrostatic adsorption to make the coating more evenly attached to the backpack, greatly improving waterproof performance and appearance quality. In addition, the installation process of waterproof zippers cannot be ignored. Waterproof zipper is one of the important components of waterproof backpack, and its installation quality directly affects the overall waterproof performance of the backpack. Professional factories will use special installation equipment and processes to ensure that the zipper is tightly integrated with the backpack fabric, while ensuring the smoothness and durability of the zipper. After the installation of the zipper is completed, a strict waterproof test will be conducted to ensure that there is no water leakage in the zipper area. In summary, to evaluate the waterproof technology capability of a waterproof backpack factory, it is necessary to comprehensively consider its professional level in the application of waterproof materials and waterproof processes. Only with strong waterproof technology capabilities can factories produce backpack products with excellent waterproof performance and reliable quality, meeting the growing demand for waterproof backpacks in the market.
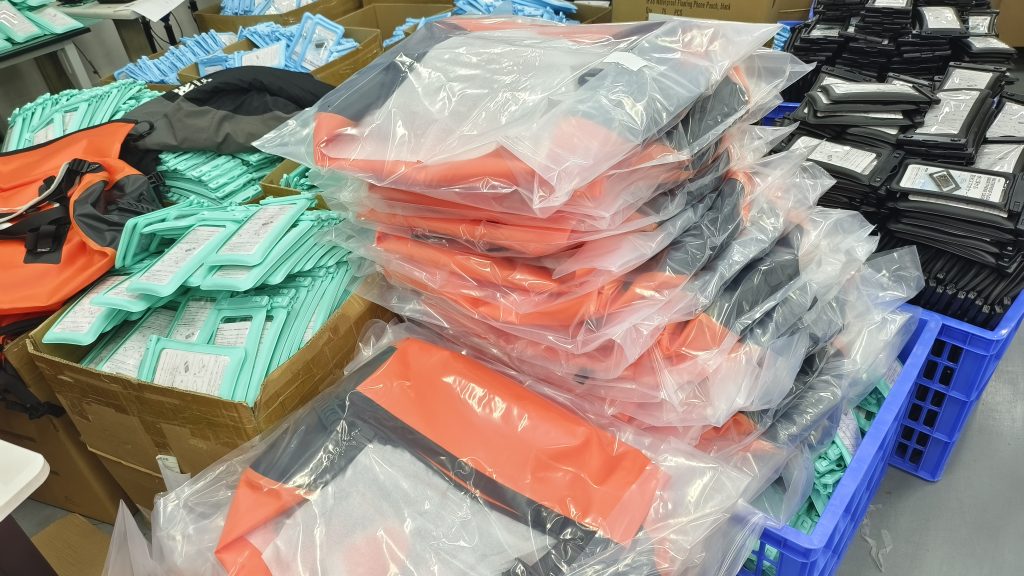
The level of sewing technology, proficiency in backpack sewing, backpack sewing is a delicate and critical process, and its quality directly affects the overall quality and durability of waterproof backpacks. Skilled sewing techniques can ensure that the various parts of the backpack are tightly connected, not only enhancing the structural stability of the backpack, but also improving its waterproof performance. Experienced workers have a precise grasp of needle and thread selection as well as sewing speed when sewing waterproof backpacks. For example, when sewing key parts such as the backpack body and straps, double needle or multi needle sewing technology is used to increase the firmness of the stitching and prevent the straps from falling off during frequent use. Meanwhile, fine and uniform stitches can reduce gaps and lower the risk of water leakage. Generally speaking, backpacks sewn by high-quality factories have a reasonable number of stitches per inch, which ensures sewing strength and does not affect the waterproof performance of the fabric due to excessive needle holes. In addition, workers need to adjust sewing parameters for fabrics of different materials. When sewing lightweight waterproof fabrics, the sewing speed should be appropriately reduced to avoid wrinkling or needle piercing of the fabric; For thick and durable fabrics, thicker sewing threads and suitable machine needles should be used to ensure a smooth and secure sewing process. The maturity of the laminating process plays a crucial role in the manufacturing of waterproof backpacks. It is mainly used to seal the seams of backpacks and prevent moisture from seeping into the gaps between the seams. The proficiency of the factory in the glue pressing process directly determines the waterproof effect of the backpack. Mature adhesive technology requires factories to have advanced adhesive equipment and professional operators. The control of temperature, pressure, and time is crucial during the gluing process. The appropriate temperature can fully melt and evenly distribute the glue, while pressure ensures a tight bond between the glue and the fabric, and precise time control can ensure the stability of the bonding effect. For example, some high-end waterproof backpack factories use computer numerical control glue pressing equipment, which can accurately control these parameters, making the glue width and thickness uniform and consistent, effectively improving the waterproof performance at the joints. At the same time, quality inspection of the adhesive is also an indispensable part. Professional factories will conduct strict inspections on the seams of each backpack after the glue pressing is completed, checking for issues such as bubbles, delamination, or incomplete glue pressing. For products that do not meet the standards, timely rework will be carried out to ensure that every waterproof backpack leaving the factory has reliable waterproof performance. In summary, the proficiency of factories in key processes such as backpack sewing and glue pressing is an important indicator to measure their technical strength and process level. Only by striving for excellence in these technological processes can we produce high-quality and high-performance waterproof backpack products.
In the fiercely competitive waterproof backpack market, the innovative research and development capabilities of factories are the core driving force for promoting product upgrades and sustainable development of enterprises. The level of R&D investment is an important indicator for measuring a factory’s determination and potential for innovation. A waterproof backpack factory with forward-looking vision will invest a considerable proportion of funds in the research and development of new materials and processes. These funds are not only used to purchase advanced research and development equipment, such as material testing instruments, simulation environment test chambers, etc., in order to more accurately research and develop new materials and processes, but also to attract and cultivate high-quality research and development talents. A professional R&D team is the source of innovation, as they are able to continuously explore cutting-edge technologies in the industry and provide strong support for product innovation in factories. For example, some well-known waterproof backpack factories allocate a certain proportion of their annual sales to research and development projects, which enables them to keep up with the pace of technological development and continuously launch innovative products. This continuous investment ensures that the factory maintains a leading position in the field of technology, and is able to take the lead in applying new materials and advanced processes to the production of waterproof backpacks, meeting the market’s continuous pursuit of high-quality and high-performance products. In addition to R&D investment, the ability to transform R&D results is equally crucial. An excellent waterproof backpack factory not only needs to have strong research and development capabilities, but also needs to be able to quickly and effectively transform research and development results into actual products and push them to the market. The successful transformation of research and development achievements is reflected in multiple aspects. In terms of new material research and development, factories may develop waterproof fabrics with unique properties, such as waterproof materials with self-cleaning function, which can effectively prevent stains from adhering, keep the appearance of backpacks clean, and provide consumers with a more convenient user experience. By applying such new materials to product production, factories can launch waterproof backpacks with differentiated competitive advantages, attracting more consumer attention. In terms of the transformation of new process research and development achievements, for example, the factory has developed a new seamless welding process, which can further improve the waterproof performance and overall structural strength of backpacks. By applying this process to actual production, not only does it improve product quality, but it may also optimize the production process, reduce production costs, and thus enhance the market competitiveness of the product. In addition, the transformation of research and development achievements is also reflected in the rapid response to market demand. By closely monitoring market trends and consumer feedback, factories are able to timely integrate research and development results with market demand, and launch new products that are in line with market trends. This agile ability to transform research and development results enables factories to take the initiative in market competition and continuously explore new market shares. In summary, innovative research and development capabilities are an important reflection of the technical strength and process level of waterproof backpack factories. The investment and achievement transformation ability of factories in the research and development of new materials and processes not only determine the innovation and competitiveness of their products, but also relate to the long-term development prospects of the enterprise. Therefore, when selecting a waterproof backpack factory, enterprises should focus on examining the factory’s innovative research and development capabilities, and choose factories with strong research and development capabilities and efficient results transformation capabilities as partners to jointly promote technological progress and product upgrades in the waterproof backpack industry.
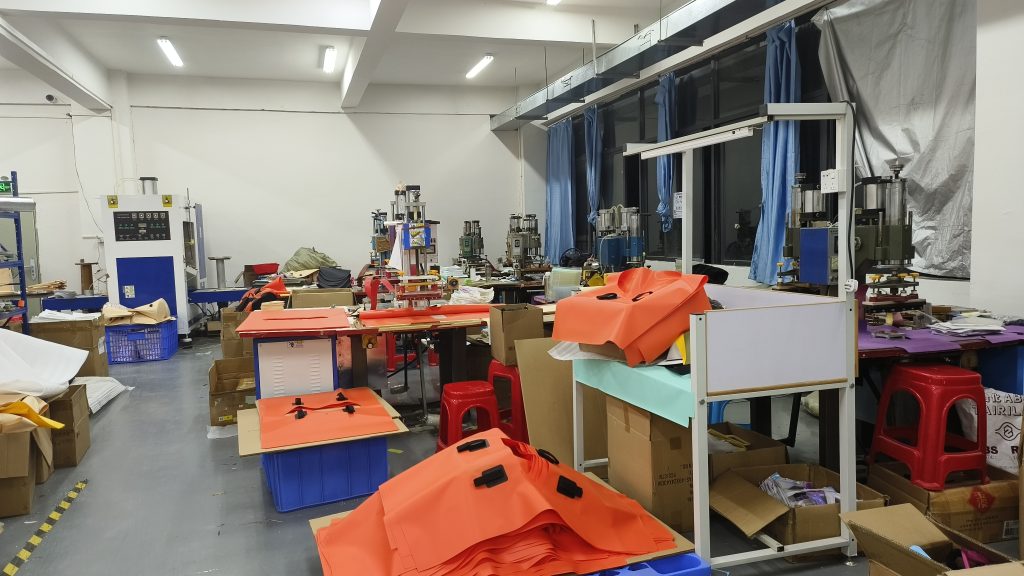
In today’s diversified market environment, the demand for customized waterproof backpacks from enterprises is increasing. From the appearance design to functional configuration of backpacks, different customers have various unique requirements. At this point, the factory’s ability to respond to customized demands becomes particularly critical. Excellent waterproof backpack factories will view customers’ customized needs as opportunities to enhance their competitiveness, rather than burdens. They have a professional design team that can communicate deeply with clients, fully understand their creativity and ideas, and transform them into feasible design solutions. Whether it is in the color, pattern, material matching of the backpack, or in the design of the internal structure and storage function, personalized customization can be carried out according to the specific needs of customers. For example, some companies may want to add unique brand logos or promotional elements to waterproof backpacks, and professional factories can perfectly integrate these elements into backpack design through advanced printing or embroidery techniques, while ensuring its quality and durability. For some functional customization needs, such as adding special pockets, using specific zippers or fasteners, factories can also provide practical and feasible solutions with rich experience and technical strength. In addition, flexible factories will maintain close communication with customers during the customization process, provide timely feedback on design and production progress, adjust and optimize according to customer feedback, and ensure that the final product fully meets customer expectations. This cooperative attitude of actively responding to customized needs not only meets the personalized needs of customers, but also enhances their trust and satisfaction with the factory, laying a solid foundation for long-term cooperation between both parties. In addition to customized requirements, the willingness to produce in small batches is also an important indicator for measuring the flexibility of factory cooperation. For some emerging brands, startups, or enterprises conducting specific marketing activities, the demand for small-scale production of waterproof backpacks is more common. These enterprises may not be able to place large-scale production orders due to financial constraints, market testing needs, or rapid product updates. Factories with flexible cooperation will fully consider the needs of these enterprises and are willing to undertake small-scale production orders. Although small-scale production may increase production costs and management difficulties for factories, such factories will optimize production processes, allocate resources reasonably, and minimize the cost of small-scale production while ensuring product quality, providing customers with cost-effective solutions. At the same time, for small batch production orders, factories will also give sufficient attention and will not lower production standards or service quality due to small order quantities. From raw material procurement, production process control to quality inspection, we strictly follow standard procedures to ensure that every small batch of waterproof backpacks can meet high-quality requirements. This cooperative attitude of willing to grow together with customers and support small batch production can provide strong support for enterprises in the development stage, promoting mutual benefit and win-win results for both parties. The diversity of cooperation methods and the flexibility of cooperation are also reflected in the factory’s ability to provide diverse cooperation methods. In addition to the traditional labor and material production model, some factories can also provide cooperative methods such as processing with supplied materials and samples according to customer needs. In the incoming material processing mode, customers provide raw materials, and the factory uses its own production equipment, technology, and labor to carry out production and processing. This cooperation method is suitable for customers who have specific requirements for raw materials or have established stable raw material supply channels. The factory relies on its professional production capacity to ensure that raw materials can be efficiently and accurately processed into waterproof backpacks that meet quality standards. Sample processing refers to the customer providing samples, and the factory produces according to the style, material, process, and other requirements of the samples. This cooperation method tests the factory’s replication and production capabilities, and can meet customers’ needs for quickly launching similar products or making product improvements. In addition, some factories will also carry out joint development projects with customers, jointly investing resources in the research and design of new products. By integrating the strengths of both parties, innovative products can be brought to market faster, achieving sharing of technology, market, and benefits between both parties. This diversified cooperation approach can meet the needs and preferences of different customers, enhance the cooperation stickiness between factories and customers, and create more opportunities and value for both parties.
Summary of Key Points for Factory Selection: When selecting a waterproof backpack factory, it is necessary to comprehensively consider multiple core elements to ensure that the selected factory meets its own development needs and guarantees product quality and supply stability. At the level of production capacity, attention should be paid to capacity matching, factory scale, and production line configuration. The production capacity needs to be dynamically matched with the order demand, taking into account the production cycle; Large scale factories are conducive to standardized production and cost control, while small-scale factories excel in flexibility; Modern production lines can improve quality, efficiency, and control costs. In terms of technology and craftsmanship, waterproof technology, sewing technology, and innovative research and development capabilities are indispensable. Waterproof technology covers material application and process level, ensuring the waterproof performance of backpacks; Proficient sewing and gluing techniques are crucial for the quality and durability of backpacks; Strong innovation and research capabilities drive product upgrades and enhance market competitiveness. The quality control system is crucial, including the quality management system, testing equipment configuration, and quality traceability mechanism. A sound quality management system ensures production standards, advanced testing equipment ensures product compliance, and a sound quality traceability mechanism can locate the source of problems and reduce losses. Supply chain management capability is equally important, involving inventory management, delivery capability, and raw material procurement. Reasonable inventory management optimizes production and costs, timely and reliable delivery ensures market supply, strong raw material procurement capabilities ensure quality and control costs. Corporate reputation and cooperation attitude cannot be ignored, reflected through industry reputation, cooperation flexibility, and after-sales service. Good reputation reflects the strength and image of the factory, flexible cooperation meets diverse needs, and high-quality after-sales service enhances customer trust and cooperation stability.
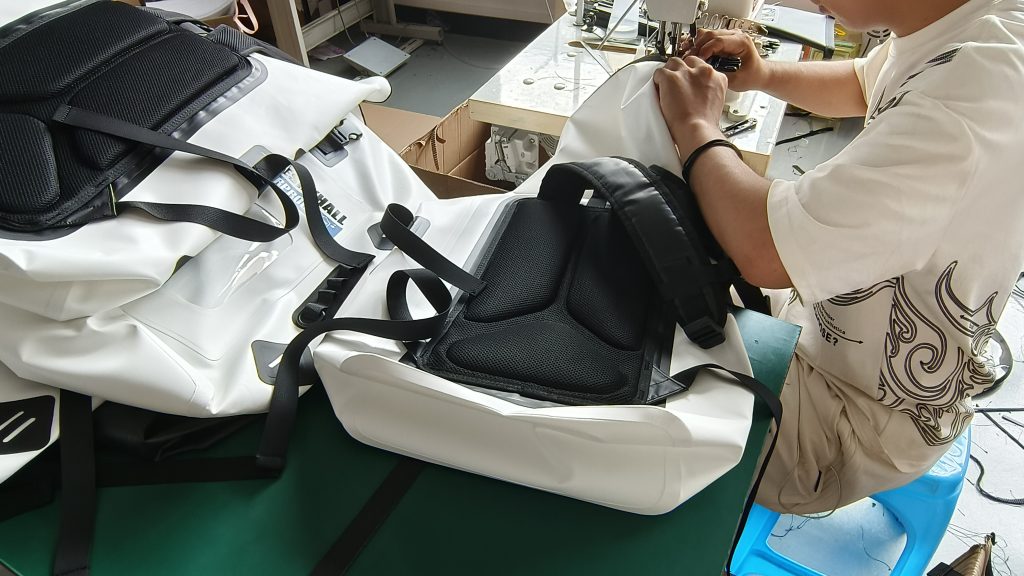
waterproof backpack new,waterproof backpack nike,waterproof backpack north,waterproof backpack oakley,waterproof backpack on,waterproof backpack yellow factoriespatagonia waterproof backpack,waterproof backpack purse,waterproof backpack purple,waterproof backpack 5.11waterproof roll top backpack,waterproof backpack rain,waterproof backpack roll,waterproof backpack red,waterproof backpacks,small waterproof backpack,sling backpack waterproof,waterproof small backpack women,tactical backpack waterproof,waterproof backpack 5.11travel backpack waterproof,the north face waterproof backpack,backpack waterproof usb business bag,waterproof backpack used,waterproof backpack under,waterproof backpack up,waterproof backpack usa,waterproof backpack yellow factorieswaterproof backpack vintage,waterproof backpack 40lwaterproof backpack vera,waterproof backpack xl,waterproof backpack xxl,waterproof backpack x small,waterproof backpack 5.11x waterproof backpack cover,yeti waterproof backpack,waterproof backpack yellow,waterproof backpack yellow factorieswaterproof backpack yeti,waterproof backpack zero,waterproof backpack zip,waterproof backpack zipper,waterproof backpack 15,waterproof backpack 25l,waterproof backpack 20l,waterproof backpack 40l2 waterproof backpack men,waterproof backpack 30l,waterproof backpack 40l,waterproof backpack 45l,waterproof backpack 5.11,6 waterproof backpack women,7 waterproof backpack women,8 waterproof backpack men,8 waterproof backpack women,waterproof backpack 40l9 waterproof backpack men,9 waterproof backpack cover,