The research objective is to highlight the importance of motorcycle travel equipment in the increasingly popular trend of motorcycle travel. Among them, the car tail bag, as an indispensable part, directly affects the riding experience in terms of quality, customized functions, and the value it contains. However, facing numerous motorcycle tailpack manufacturing factories in the market, how to make the appropriate choice has become a challenge for motorcycle enthusiasts. This article aims to deeply analyze the selection criteria for motorcycle tail bag production factories, helping motorcycle enthusiasts find the perfect balance between quality, customization, and value, and selecting high-quality tail bag production factories that can meet their own needs and improve cycling quality, making every motorcycle trip more comfortable, enjoyable, and reassuring. The level of production technology plays a decisive role in the quality of the motorcycle rear end package. Firstly, there is the sewing technique, which is the fundamental step in the production of tail bags. High quality factories will use advanced sewing equipment and exquisite sewing techniques to ensure that every stitch is even and tight. For example, fine stitches not only enhance the overall firmness of the tail package, but also effectively prevent rainwater from seeping in through the pinholes. At the same time, key areas such as the shoulder strap connection and zipper edges will be reinforced with sewing technology to increase the durability of these easily worn areas, in order to withstand frequent shaking and pulling during the friction process. Material handling capability is also an important indicator for measuring the manufacturing process of a factory. In the cutting process, precise cutting can minimize material waste and ensure the accuracy of the dimensions of each component, so that the tail package can fit the motorcycle and have a smooth appearance after assembly. For materials of different materials, factories should have corresponding pre-treatment capabilities. For example, some fabrics may require waterproof coating treatment, UV protection treatment, etc. to enhance the functionality of the tail bag. In addition, leather materials may require special treatments such as softening and maintenance to make them soft, comfortable, and resilient enough to extend their service life. The hot pressing process is becoming increasingly common in the production of modern motorcycle tail bags, which can shape the specific shape of the tail bag and enhance structural stability. Excellent factories can precisely control the temperature, pressure, and time of hot pressing, ensuring that the shape of the formed tail package is neat and the lines are smooth, without damaging the performance of the material. In addition, details can better showcase the manufacturing process level of the factory. Like edge wrapping, if the factory adopts a fine edge wrapping process, it can not only beautify the appearance of the tail package, but also prevent the fabric edges from coming loose, improving the overall quality of the tail package. The installation of hardware accessories, with a firm and smooth installation process, can ensure that hardware such as zippers and fasteners are not easily loose or damaged during long-term use, providing convenience for motorcycle riders. In short, the level of production technology covers multiple aspects, and only factories with high-level production technology can produce high-quality motorcycle rear end bags. Durability and waterproofness: During the journey, the changing weather and complex road conditions place strict requirements on the durability and waterproofness of the car’s tail bag. Therefore, the quality of materials selected by the factory is crucial. Fabric is the core element that determines the durability and waterproof performance of the tail bag. High quality factories tend to use professional outdoor fabrics, such as high-strength nylon fabrics. This fabric not only has excellent wear resistance and can resist common injuries such as tree branch scratching and stone impact during the rubbing process, but also performs excellently in terms of waterproof performance. Some advanced nylon fabrics have undergone special waterproof treatment and have good waterproof and breathable properties. They can effectively block rainwater infiltration and allow the moisture inside the tail bag to dissipate, preventing items from getting damp due to the accumulation of moisture. In addition, polyester fiber fabric is often used for tail bag production, which has the characteristics of good wrinkle resistance and shape retention. While ensuring durability, it can keep the tail bag in a good shape at all times. The zipper, as a frequently used component of the tail bag, directly affects the user experience and waterproof effect of the tail bag. High quality factories usually choose well-known brand zippers, such as YKK zippers. These zippers have high-precision tooth bite design, smooth and durable pulling, and can withstand a large number of opening and closing operations without being easily damaged. At the same time, zippers with waterproof function are an ideal choice for motorcycle tail bags. This type of zipper, with a special sealing structure and coating treatment, can effectively prevent moisture from seeping into the interior of the tail bag through the zipper gaps even when exposed to rainwater for a long time. Stitching cannot be ignored either, it is like the “bones” of the tail package, connecting various parts. High quality sutures should have sufficient strength and water resistance. The factory will use high-strength polyester thread specially designed for outdoor products. This thread not only has strong tensile strength, but also ensures that the stitching does not crack when the tail package is subjected to heavy objects and bumps. It also has good weather resistance and water resistance, which can prevent the stitching from aging and breaking due to rainwater erosion. In key areas such as the corners of the tail bag and the connection of the straps, factories often use double or multiple seam processes to further enhance the firmness of the stitching and improve the overall durability of the tail bag. In summary, the factory fully considers durability and waterproofness in the selection of materials such as fabrics, zippers, and stitching, which is the key to producing car tail bags that can withstand the test of motorcycle travel.
In the current emphasis on sustainable development and personal health and safety, environmental protection and safety standards cannot be ignored. Whether the materials selected by the motorcycle tail bag manufacturing factory meet environmental requirements and safety usage standards cannot be ignored. On the environmental level, materials that meet environmental standards mean that their negative impact on the environment is minimized throughout their entire lifecycle, from raw material acquisition, processing and production to final disposal. For example, some factories use fabrics made from naturally degradable fibers or employ environmentally friendly dyeing techniques in the production process, significantly reducing the use of chemical agents and minimizing water pollution. After completing its mission, such materials can decompose relatively quickly in the natural environment, reducing the accumulation of garbage. From the perspective of safety usage standards, the tail bag of a motorcycle may come into close contact with the human body, especially during cycling, where the user may touch the tail bag for a long time. Therefore, the material must be non-toxic and harmless, and not cause irritation to the skin. For example, if inferior leather or synthetic leather containing harmful substances is used for the shoulder strap that comes into direct contact with the skin, it may cause skin allergies and other problems. High quality factories will strictly control the source of materials, ensure that leather undergoes environmentally friendly treatments such as chromium free tanning, remove possible heavy metals and harmful chemicals, and ensure the health and safety of users. In addition, materials that may come into contact with items inside the tail package should not release harmful substances. Especially when storing food, electronic products, and other items, if the packaging material contains harmful substances such as volatile organic compounds (VOCs), it may contaminate the food and affect physical health; Or it may cause corrosion, interference, and other damage to electronic devices. Therefore, materials that meet safety usage standards should have good chemical stability and not easily release harmful substances. At the same time, some factories also consider fire resistance in material selection. During the motorcycle journey, the temperature near the engine of the vehicle is high. If the tail package material is flammable, it is highly likely to cause a fire if exposed to open flames or high temperatures. Therefore, materials with certain fire resistance can add a guarantee to cycling safety. A motorcycle tail bag manufacturing factory that values material environmental protection and safety standards not only reflects a sense of responsibility for the environment, but also respects and cares for the health and safety of consumers. This is also an important dimension for measuring whether a factory is trustworthy. Only by selecting materials that meet environmental requirements and safety standards can motorcycle enthusiasts enjoy the fun of cycling without any worries. Sample production and modification: The sample production process of a professional motorcycle tail bag manufacturing factory should be standardized and rigorous. After receiving customized requirements from customers, a professional project team will first have in-depth communication with the customer to understand their specific requirements for the size, shape, function, material, and other aspects of the final package. These requirements will be organized into clear and concise production documents. Subsequently, the design department quickly launched the design work based on these requirements, using advanced design software to draw detailed drawings of the final package, including views from various angles, internal structure, and detailed design, ensuring that every detail can be accurately presented on the drawings. After the completion of the drawings, a strict review process will be carried out, with experienced designers and technical experts jointly checking whether the design meets customer needs, production process requirements, etc., to avoid design defects in the later stage. The approved design drawings are transferred to the sample production workshop, and workshop staff select suitable materials based on the drawings. At this point, precise matching of materials is crucial, as it is necessary to ensure that the material characteristics meet the usage scenarios and customer requirements of the final package, while also ensuring that the material quality is superior. After selecting the materials, the cutting process begins. With the help of high-precision cutting equipment, the materials are precisely cut according to the design dimensions to ensure that the dimensional errors of each component are controlled within a very small range. Next is the sewing and assembly stage, where skilled workers use their exquisite sewing skills to meticulously sew the cut parts according to the design requirements. In this process, special attention will be paid to the sewing process of key parts, such as using reinforced sewing, double or multiple sewing techniques, to ensure the firmness of the tail package. At the same time, when installing hardware accessories such as zippers and fasteners, the installation quality will be strictly controlled to ensure that the hardware is installed firmly and used smoothly. Finally, the assembled samples will undergo comprehensive quality testing. The testing content includes visual inspection to check for defects, loose threads, stains, etc; Measure the dimensions to ensure that the dimensions of each part meet the design requirements; Functional testing to verify whether the zipper opening and closing of the tail bag are smooth, whether the strap adjustment is flexible, and whether the various storage spaces are practical. Only samples that have passed strict testing will be delivered to customers. When customers provide modification suggestions for samples, the response speed and modification efficiency of the factory become particularly important. Efficient factories will immediately establish a dedicated feedback processing team to conduct detailed analysis and evaluation of customer feedback and modification suggestions. The team members include designers, technicians, and production supervisors, who will assess the feasibility of modification suggestions from different professional perspectives and develop specific modification plans. Once the revised plan is confirmed, the relevant departments will take prompt action. The design department promptly adjusts the design drawings and accurately reflects the modified content on the new drawings. The procurement department quickly procures additional or replacement materials required based on new design requirements to ensure timely material supply. The sample production workshop modifies the samples as quickly as possible according to the new drawings and modification plans. During the modification process, the staff will strictly control the quality to ensure that the modified parts are perfectly integrated with the original parts, without affecting the overall performance and aesthetics of the final package. Throughout the entire modification process, the factory will establish an effective communication mechanism to provide timely feedback to customers on the progress of the modifications, allowing them to stay informed of the sample modifications at any time. Generally speaking, for some simple modifications, the factory can complete them in a shorter period of time and resubmit them to the customer for review; For more complex modifications, we will also arrange the time reasonably, complete the modification tasks with high quality within the promised deadline, and maximize the satisfaction of customer needs, demonstrating a good service attitude and professional ability. This efficient sample production and modification process and capability can help motorcycle enthusiasts quickly obtain tail bag samples that meet their preferences, laying a solid foundation for subsequent mass production.
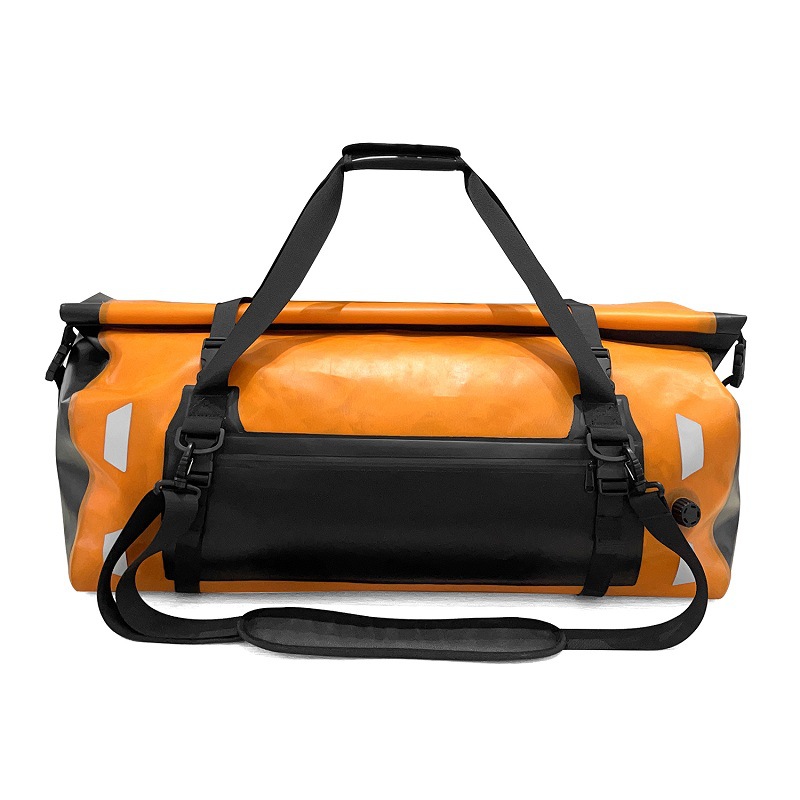
For large-scale orders, different motorcycle and travel car tail bag production factories will offer various preferential policies. Some factories will directly offer discounts on the unit price, and the more orders there are, the greater the discount. For example, when the order quantity reaches 50, each tail package can enjoy a 5% price discount; If the order quantity increases to 100, the discount may expand to 10%. This direct price concession can save significant costs for the purchaser. Some factories will also offer additional products as gifts. For example, for every purchase of a certain quantity of tail bags, additional tail bag accessories such as rain covers and mounting tools will be given as gifts. Although the individual value of these gifts may not be high, for bulk buyers, the accumulation of small amounts can also reduce the overall procurement cost, enrich product matching, and enhance the practicality and attractiveness of the products. Additionally, some factories offer discounts on shipping costs. For large-scale orders, the factory bears all or part of the shipping costs, which is also a significant cost savings for the purchaser. Especially when the purchase quantity is large and the transportation distance is long, freight discounts can significantly reduce the pressure on procurement costs. The ability to control costs reflects the factory’s ability to provide batch production discounts, which relies on its strong cost control capabilities. In the process of raw material procurement, large-scale orders give factories stronger bargaining power when negotiating with suppliers. Factories can obtain lower raw material prices from suppliers by relying on a large amount of procurement demand, thereby reducing the raw material cost per unit product. For example, by signing long-term large purchase contracts with fabric suppliers, factories can obtain the required fabrics at a price 15% or 20% lower than small batch purchases. In the production process, mass production helps to improve production efficiency and share fixed costs. With the expansion of production scale, the utilization rate of equipment is improved, and fixed costs such as equipment depreciation and factory leasing allocated per unit product will be reduced. At the same time, workers become more skilled in repetitive production processes, resulting in faster production speeds and lower defect rates, further saving production costs. For example, originally producing one tail package required 2 hours of manual labor time. In the mass production process, by optimizing the production process and improving worker proficiency, the manual labor time for a single tail package can be reduced to 1.5 hours, greatly reducing labor costs. In addition, efficient supply chain management is also key to cost control. The factory reduces inventory backlog and stockouts by planning inventory reasonably, and lowers inventory management costs. At the same time, optimize the logistics distribution process, integrate transportation resources, improve transportation efficiency, and reduce logistics costs. These comprehensive cost control measures provide the factory with sufficient space to offer preferential policies for large-scale orders while ensuring product quality, achieving a win-win situation for both the factory and the purchaser. When choosing a factory, motorcycle enthusiasts should not only pay attention to preferential policies, but also consider the factory’s cost control ability, as this is related to the long-term quality stability and price rationality of the product. Quality assurance policy, warranty period commitment, warranty period is an important indicator to measure a factory’s confidence in the quality of its own products. There are differences in the warranty period set by different motorcycle tail bag manufacturing factories. Some factories with strong capabilities and strict control over product quality will provide a longer warranty period, usually 2-3 years. This means that during this period, if there are quality problems caused by non-human factors in the tail package, the factory will bear the corresponding responsibility for repair or replacement. For example, in normal use, if the zipper of the tail bag is damaged, the stitching is torn, or the fabric is damaged, the factory will provide free repair or directly replace it with a new product. However, some factories may offer a relatively short warranty period, around one year. Although the length of the warranty period does not necessarily equate to product quality, a longer warranty period undoubtedly provides consumers with more protection, reflecting the factory’s high confidence in its production process and product quality. When there are quality issues with the final package, the simplicity and efficiency of the factory’s after-sales processing process directly affect consumer satisfaction. A high-quality factory will establish a comprehensive and standardized after-sales processing mechanism. Firstly, after consumers discover problems and submit after-sales applications, the factory will establish a dedicated customer service channel to ensure timely response. Customer service personnel will record in detail the issues reported by consumers, including specific manifestations of problems with the tail package, purchase time, usage information, etc., and guide consumers to provide necessary photos or video materials to more accurately determine the nature of the problem. Next, the factory will quickly organize professional technical personnel to evaluate the feedback issues. If the problem is relatively simple and clear, and falls within the scope of warranty, technicians will immediately develop a solution, such as arranging repairs or replacing with new products. For some complex problems, technicians will conduct in-depth analysis to determine whether it is due to design or production defects in the product itself, or other reasons such as improper use by consumers. If it is determined to be a product quality issue, the factory will arrange for repair or replacement work as soon as possible. In terms of maintenance, the factory will use original genuine parts to ensure that the performance and quality of the repaired tail package are not affected. For situations where new products need to be replaced, the factory will ship them in a timely manner to minimize the waiting time for consumers. Throughout the entire after-sales process, the factory will maintain close communication with consumers, promptly informing them of the progress of problem handling and keeping them informed of whether their demands have been properly resolved. At the same time, the factory will track and summarize after-sales issues in order to continuously improve product design and production processes, and avoid similar problems from happening again. This comprehensive and efficient after-sales processing process can not only solve consumers’ practical problems, but also enhance consumers’ trust and loyalty to the factory, and establish a good brand image. When choosing a factory, motorcycle enthusiasts should focus on its quality assurance policy and after-sales processing procedures to ensure that they can enjoy reliable after-sales service guarantee after purchasing the final package.
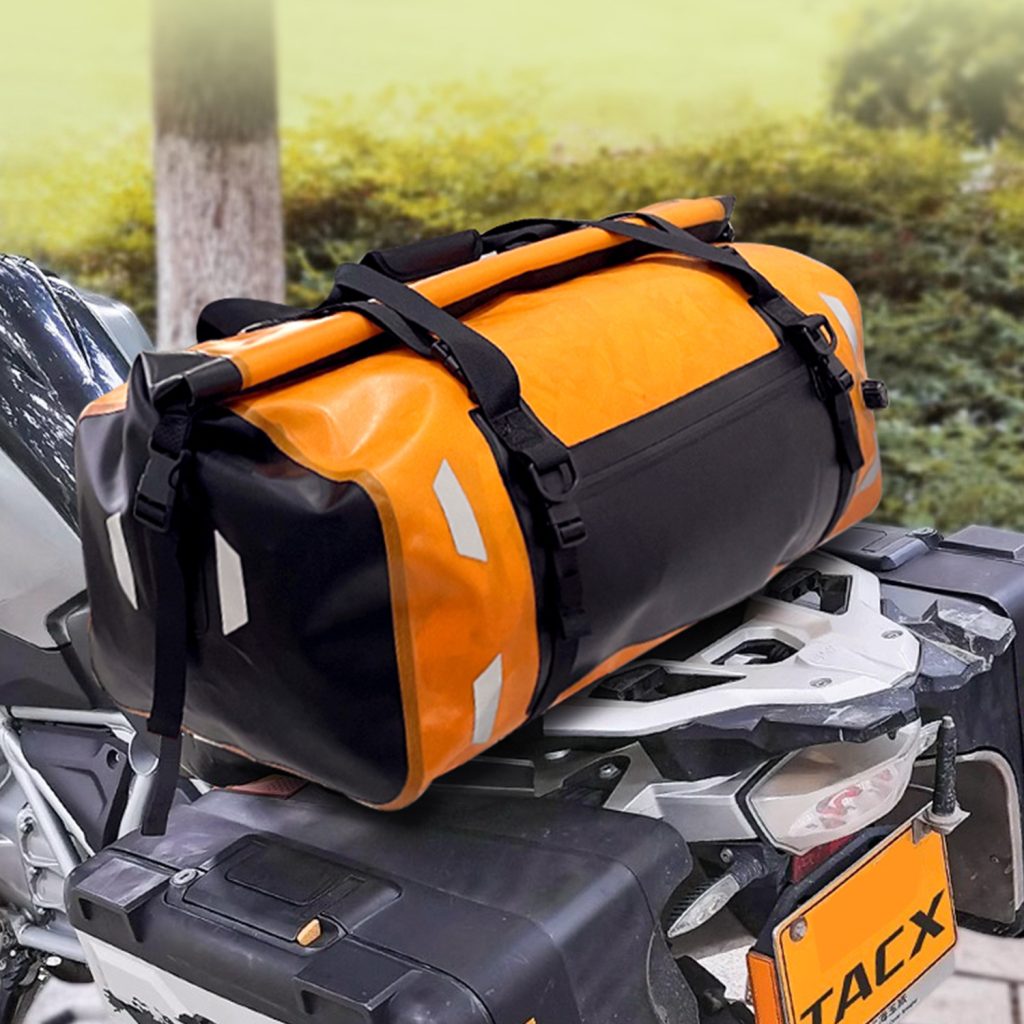
waterproof motorcycle saddlebags,waterproof bike seat,motorcycle waterproof bag,motorcycle waterproof bag small,amphibious drytools waterproof motorcycle tool bag,augrex waterproof motorcycle handlebar bag,motorcycle tail bag waterproof motorcycle bags australia waterproof backpack abs hard shell,waterproof motorcycle bag,motorcycle tail bag waterproof,motorcycle handlebar bag waterproof,motorcycle crash bar bag waterproof,waterproof waterproof motorcycle bags australia compression bags motorcycle camping,waterproof motorcycle saddle bag covers,motorcycle duffle bag waterproof,motorcycle dry bags waterproof,waterproof dry bags for motorcycle travel,motorcycle fork bag motorcycle waterproof duffel bag distributorwaterproof,waterproof gear bag motorcycle,waterproof motorcycle helmet bag,ustpo motorcycle backpack waterproof bag hard shell,kemimoto motorcycle waterproof tank bag,kronox motorcycle waterproof duffel bag,waterproof motorcycle luggage bags,motorcycle travel bags formotorcycle waterproof duffel bag distributor sissy bar luggage rack waterproof,motorcycle leg bag waterproof,odinsberg waterproof motorcycle tail bag 7l,motorcycle pannier bags waterproof,waterproof phonewaterproof motorcycle bags australia bag for motorcycle,high-quality waterproof motorcycle back seat bag,waterproof bag for motorcycle luggage rack,motorcycle rear seat bag waterproof,motorcycle camping waterproof bagtank bag for motorcycle waterproof,tacx 4-in-1 waterproof motorcycle tail bag,110l waterproof duffle bag motorcycle,dry duffle bags waterproof motorcycle 20l,motorcycle waterproof duffel bag 30l,motorcycle camping waterproof bag3p military duffel waist bag molle bicycle/motorcycle waterproof,waterproof motorcycle bag 40l,rockbros waterproof duffel bag 60l motorcycle travel,motorcycle duffle bag 70l waterproof,motorcycle waterproof duffel bag distributormotorcycle waterproof bag,best motorcycle waterproof bag,motorcycle waterproof bags uk,motorcycle waterproof bags for sale,large motorcycle waterproof bags,motorcycle tail bag waterproof,motorcycle camping waterproof bagwaterproof motorcycle luggage rack bags,waterproof saddle bag for motorcycle,motorcycle leg bag waterproof,waterproof motorcycle helmet bag,